La simulation CNC est une ressource extrêmement précieuse car elle a le pouvoir de planifier et de vérifier l’usinage à contrôle numérique. Cela comprend tous les composants que l’on trouve dans l’environnement logiciel de CAO et de FAO. En d’autres termes, vous pouvez « prévoir l’avenir » de votre usinage et optimiser le temps, le processus et les ressources.
Cette technologie mémorise toutes les machines, les accessoires et les systèmes de serrage avec précision et en temps voulu dans l’environnement de production virtuel. La simulation crée des copies numériques avec tous les composants.
Grâce aux résultats de la simulation CNC, le processus devient non seulement plus sûr, mais aussi plus efficace. En effet, cette technologie est capable de détecter les éventuelles collisions ou plus généralement les problèmes qui pourraient survenir au cours du processus.
Toutes les machines à contrôle numérique les plus courantes, comme par exemple les tours avec outils motorisés, les tours multitâches, les outils de forage de trous profonds et les robots anthropomorphes avec axes supplémentaires, se prêtent parfaitement à ce type de simulation.
L’optimisation des programmes CNC offre une variété d’options qui peuvent être sélectionnées et définies dans chaque cas en fonction des conditions d’usinage. Par exemple, vous pouvez changer la machine, les outils ou la tête de la machine, modifier les paramètres de réglage, adapter la rotation des axes ou même l’orientation de la tête.
Le potentiel de la simulation CNC
Prenons l’exemple du logiciel de simulation Vericut proposé par la société californienne CGTech.
L’une de ses particularités est de pouvoir recréer virtuellement l’environnement de travail de la machine-outil réelle.
Dans ce logiciel, en effet, il est possible de :
- importer les modèles géométriques pour déterminer quelles sont les dimensions globales à contrôler ;
- définir la cinématique de la machine ;
- charger l’émulation de la commande numérique ;
- mettre en œuvre toutes les personnalisations relatives à la machine-outil individuelle, telles que les variables, les sous-programmes, les macros, les codes M.
Il faut savoir que la machine virtuelle utilisée au quotidien pour effectuer des opérations telles que l’usinage avec enlèvement de copeaux est équipée exactement comme la machine réelle. Cette technologie met en place les éléments de serrage, les différents outils, la pièce brute, les programmes de travail post-traités et exécute immédiatement le cycle de travail complet.
La simulation CNC permet en outre de comprendre combien de temps sera nécessaire pour développer l’usinage et de planifier les étapes de la meilleure façon possible. La production en bénéficiera car les temps d’usinage sur la machine CNC seront calculés automatiquement.
Rapport d’erreur et surveillance de la variation temporelle des quantités
La simulation CNC, réalisée grâce aux changements et améliorations constants de la transformation numérique dans l’industrie 4.0, est essentielle pour recevoir les rapports d’erreur pendant le fonctionnement des machines.
En effet, lors de la simulation, les mouvements d’usinage sont identifiés. Grâce à une fenêtre dédiée, les problèmes tels que les fins de course, les collisions, les imprécisions de syntaxe, etc. sont mis en évidence. Ceci est également possible grâce à la possibilité de bloquer la machine à chaque instant de la simulation CNC, afin de vérifier les avances et de contrôler le modèle obtenu.
La possibilité d’arrêter la simulation au point précis de l’erreur permet à l’utilisateur du logiciel de se familiariser facilement avec l’environnement de travail virtuel. De cette façon, il peut se rendre compte des avantages de cette approche et se sentir plus en sécurité lorsqu’il se déplacera réellement dans la machine.
En d’autres termes, la simulation CNC permet d’obtenir des jumeaux numériques qui reproduisent fidèlement tous les composants de tout environnement de production dans des bibliothèques numériques réelles.
Outre les avantages considérables en termes de contrôle des erreurs et de correction des processus, la simulation CNC maximise le retour sur investissement de l’ensemble de l’atelier.
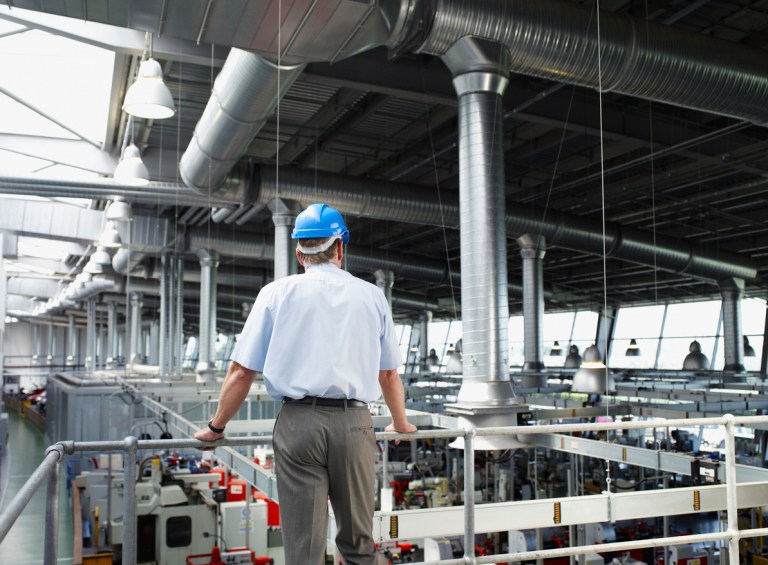
L’opérateur dispose d’un grand nombre d’informations sur la configuration de la pièce à usiner, du composant et des outils. Et comme mentionné précédemment, lorsqu’une opération d’usinage nécessite soudainement une amélioration, il est possible d’intervenir en temps réel.
Il ne faut pas non plus sous-estimer la possibilité de vérifier plusieurs fois les trajectoires des outils grâce aux post-processeurs intégrés.
En comparant le résultat de l’usinage avec le modèle original, on constate que chaque pièce usinée est parfaitement identique au modèle conçu.